|
IVO Propeller Blade Cutting Fixture
When I purchase an IVO propeller, I usually purchase reconditioned blades because of the money saved. But IVO does not always have the desired blade size, so one must purchase longer blades and cut them to the desired length.
I purchased blades for a 68 inch diameter high pitch propeller for the Victor 1+ engine. I discovered that I had to run them at a much lower pitch setting than neutral pitch. So, I purchased another set of regular blades, but IVO had just one set and they were for a 72 inch diameter propeller. I would have to cut them. I was uneasy about cutting them. After flying the 72 inch propeller on a short cross country, I decided that I must cut the blades so that it will approximate the Simonini Victor 1+ test propeller if I am going to have any chance of obtaining the fuel consumption rates published by Simonini. The Simonini test propeller was 162x114 cm or about 64 inches at 12.5 degrees pitch. To practice, I cut the high pitch IVO propeller down to 62 inches. To obtain the same 100% Simonini test propeller ideal volume displaced per one turn, I will have to set the tip pitch to 13.7 degrees.
|
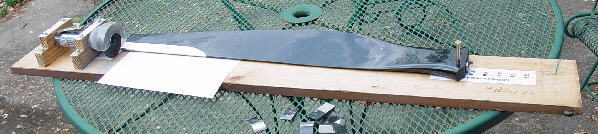
To accurately shorten each propeller blade and to maintain blade balance, I made a cutting fixture. A propeller bolt locates the leading edge hole of the blade relative to the three inch cut off abrasive wheel shown to the left. One presses down on the air motor control valve with the left hand and advances the propeller blade into the abrasive cut off wheel with the right hand. The leading edge is cut first, and care must be taken to cut slowly so that one does not over heat the epoxy/carbon fiber material. The paper under the blade is used to prevent scuffing the blade surface against the wood.
|
On the right, a scale was attached to the board to mark the distance from the cutting position to indicate finished propeller diameter. A 9/32 inch diameter holes were drilled through the board at each two inch diameter change position. The propeller bolt will self thread into this hole. If more than one inch is to be removed from the tip, the propeller blade has to be relocated with the bolt in the next hole and another cut made.
|
An inexpensive, less than ten dollars, cut off tool was purchased from Harbor Freight Tools. Mounts were made to hold the cut off wheel square with the board and so that the cut off tool rotary axis was parallel to and directly above the line on which all the propeller length indicator holes were drilled. This lets the abrasive wheel cut the propeller blade end in an arc with out excessive wear to the abrasive wheel surface next to the cut end of the propeller blade. This helps to ensure both blades will be cut to the same length, and so it is unnecessary to rebalance the blades.
|
The cut surface of the first inch cut from the blade tip. One must cut in little slow bursts, or the sparks from the metal leading edge covering will ignite and burn the epoxy underneath. Also, it is a good idea to wear a protective mask to prevent breathing epoxy and carbon dust.
|
|