|
Feeding the Rotax 447 - Fine Mid Range Bing Adjustment
How does one accommodate the change in needle slots if the change between needle slots is too great? If I run slot #2 it is too lean, if I run slot #3, it is too rich. The following is an attempt to gain finer needle adjustment.
I have been having trouble keeping the EGT's down around 1100 degrees Fahrenheit with the needle clip in the second recommended summer slot from the top of the needle. The needle drops too far and the engine is running on the lean side. As a result, the EGT's are very peaky, and one has to carefully monitor the gages to keep the temps from rising to or above 1200 degrees F. A thermal or a slight decent during cruise cause the EGT's to rise, and let down from altitude is very slow, or one must pull the engine back to an idle. Finally I realized that the 15K2 needle is not going to adapt to every application for a 447, and that what is important is to find what is the best combination for my two blade IVO prop set to limit the Rotax 447 to 6400 rpm (climb prop), and the FireFly. The first test was to place a small .016 inch thick brass washer over the needle and under the needle clip. A test flight confirmed that this was the way to go. The EGT at cruise remained 1100 degrees F. and it was very stable. I could lower the nose and drive the engine with the prop and the EGT would barely rise.
|
The small brass washer was OK for a short test but it is not suitable for long term use. This is because the needle clip must make contact with supports all located in the same plane. The small washer lifts the clip at the needle and the white plastic throttle spring retainner presses down on the clip and cants or misaligns the needle relative to the jet. If left in use for a period of time it would cause wear between the needle and the jet. To over come this problem, shims were designed that slide down in side the throttle body and come to rest on the supports for the clip.
|
Guides were added so the shim cannot rotate or bind the needle and clip assembly when the white plastic throttle spring retainer is in place. A template was make using a CAD program, printed out and attached to two strips of brass. These brass strips were purchased at the local hobby shop, and they were .016 and .032 inches thick. Adhesive was sprayed on the surface, the templates were attached, and the shims were drilled and cut out. Below, one can see the shim in place and the template. I have opened the hole through which passes the throttle cable and the retainner plug as it makes it easier to reassemble the carburetor. Using the template, one can make shims of any desired thickness.
|
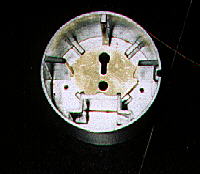
If you wish to copy this template, press the "Print Scrn" key; bring up Paint; select "Edit" and "Paste"; select "File" and "Page Setup"; set printer to landscape and "OK"; select "File" and "Print". If this does not work for you, contact me
and I can send you the cad file or a set of templates by surface mail.
|
|