Dynamic Pressure Air Filter Housing
Above the wing and just ahead of the propeller is not an optimum position for a side mounted carburetor. Static pressure above the wing is lower due to the velocity difference between above and below the wing. Also, the same is true for the air being sucked into the propeller. These two factors plus the pressure loss through the air filter medium offer some restriction to air flow to the carburetor. I thought I might recover some of the loss by capturing air stream dynamic pressure.
|
|
Full size templates were drawn for filter end plates and the housing body. These templates were sprayed with self adhesive and wall papered on to 0.009 inch thick aluminum house flashing. Next all hole centers were prick punched and drilled for 3/32 inch diameter aluminum rivets and all excess material was cut away. The holes at the little "Vees" were drilled 1/32 of an inch. These are clearance holes so that one can cut the "Vee" away and not make the material notch sensitive. This was followed by rolling and riveting the ends that will form the opening.
|
Two holes were drilled through the outer end plate and the filter to attach the plate.
Rolling the leading edges, helps to stiffen and stabilize them so they will not flex. It reduces the tendency for crack formation.
|
The flanges and/or tabs were bent on the edge of the body. Then the outer end plate was riveted to the body. The filter was inserted and riveted into place. I used six locating tabs to center the filter, and I found that these tab made it difficult to slide the filter into place. If and when I do this again, I will save a little weight and leave the locating tabs off.
Added overall weight was 1.2 ounces.
|
The inner end plate was placed over the filter mounting flange. The opening was closed and all rivets that did not pass into the filter end were put into place. At this point the assembly was placed on a drill press so that holes could be drilled into the end filter material. Drill depth was set to a little more than the rivet length. The hole furthermost away from the opening was centered and drilled and riveted first. Then the closest, followed by middle right and left, and splitting the distance.
If I was to do this over again, I would not use outer end filter locators. I would use fewer rivets, and shorten the rivet length. If I could find them, I would use smaller diameter rivets.
|
Update - 02/08/2009
Added a carburetor inlet static pressure tap to the Bing. Drilled the galley that feeds air from the inlet to the enrichener valve. Used JB Weld to hold a short 1/8 inch ID tube into the bore. This port will be used to measure inlet static pressure to see if the housing is effective.
I must wait for warmer weather to take the data.
At the same time I removed the boss on the right side of the carburetor that used to hold the Bing flip lever enrichment mechanism. Weight removed was 0.2 ounces.
|
Update - 06/26/2009 - Increase In Carburetor Inlet Pressure
A static pressure tap was installed into the filter. It is made from a 1/8 inch OD aluminum tube. The inner end is closed with a drop of JB Weld, and two small holes were drilled across the tube. Then an 1/8 inch OD hole was drilled at an angle through the filter rubber end flange to reach the inside of the filter and fixed in place with JB Weld.
|
Since I am always measuring pressure relative to something, I decided to add a reference static pressure probe to the nose cone. It is located under and forward of the ASI probes. In the future all pressure measurements will be referenced to this probe.
|
Measured pressures on a 0 to 10 inch manometer that I carried under my shoulder straps. The high pressure side was connected to the static reference probe located on the nose cone and the low pressure side connected to the probe in side the filter. I was interested to see when the pressure inside the filter switched from negative to positive as, at this point, the engine carburetor inlet would be running at the same static pressure it would see with out a filter and propeller attached to the engine.
|
The scoop was rotated at zero, 30, 60 & 90 degrees to the plane of the propeller. With the scoop straight up parallel to the propeller, the opening should sense static pressure only. This gives the base line data which represents the pressure drop across the filter material plus the air flow pressure drop of the air accelerating into the propeller. At subsequent setting of the scoop and more dynamic pressure is built up in side the housing, that the static pressure will decrease.
The reason the level is not indicating zero or 90 degrees is because the tail is on the ground and the propeller rotating plane is not vertical.
|
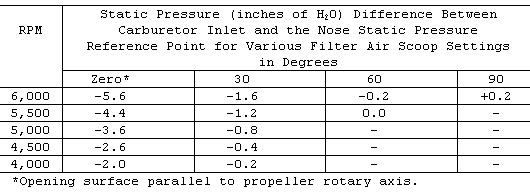
In flight data were recorded at selected rpm. Test data were taken at 2,500 feet asl in 65 degree F air. As I advanced the scoop the air fuel mixture control operation remained stable.
The increase in carburetor inlet pressure may more closely approximate Simonini engine test cell conditions. Level flight maximum engine speed increased by 200 rpm and propeller pitch was changed from 10 to 10.5 degrees at the tip. Further fuel burn rate studies are in order to see if the engine will show improvement with higher carburetor inlet pressures.
|